
An ST Engineering robotic arm drills holes in the floor grid of an airframe.
The past four years have seen commercial aircraft maintenance deal with the financial challenges of the pandemic slump in air traffic and then a difficult recovery plagued by supply chain issues, tough recruiting challenges and problems with some new engines. All these challenges will continue for a while.
But MROs are also looking to the long-term future, as growth resumes but 2050 carbon net-zero efforts put pressure on all elements of aviation to become as efficient as possible. Fortunately, there are plenty of opportunities to lean out maintenance through innovation. Indeed, there are so many innovation paths that experts say one major challenge is simply choosing the best to pursue, making the prioritization of innovations as important as implementing them.
The accompanying chart provides a menu of major innovations possible in aircraft maintenance, ranked by the priority attached to each. These priorities come from a survey of seven major MROs: three global full-service MROs, two airframe and component shops, a line maintenance company and an engine shop.
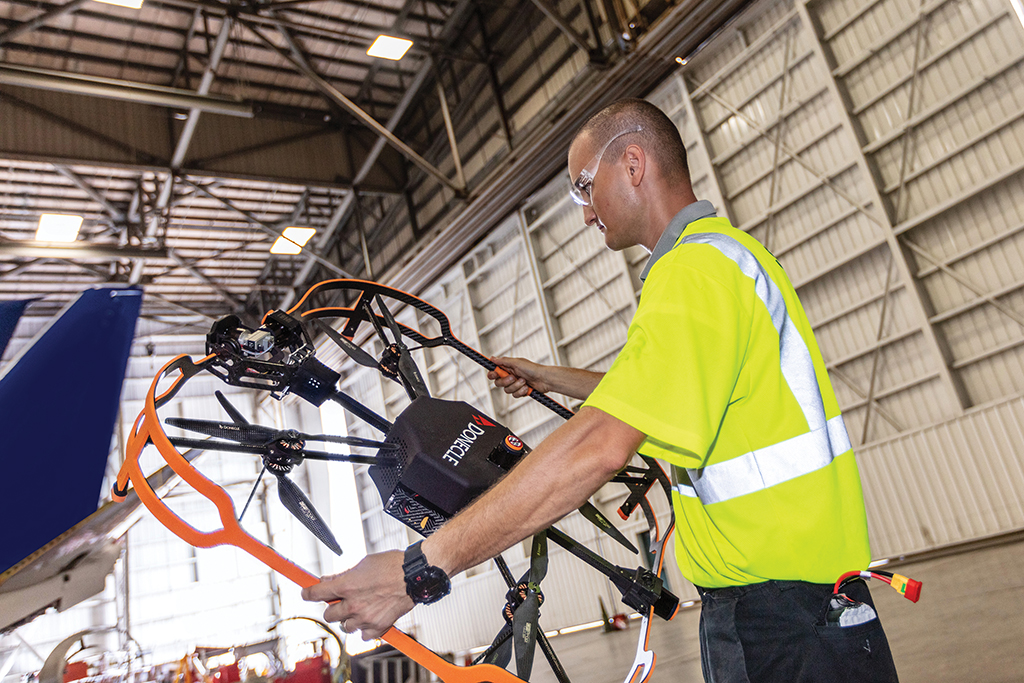
As anticipated, predictive maintenance tops the list because it cuts costs, avoids lost revenue and improves safety.
The next three innovations, digitization and two levels of artificial intelligence (AI), are enablers of many other improvements in prediction, troubleshooting, optimization and planning.
Optimizing shop processes is still important, and mergers are a non-technology enabler—they can spread innovations to smaller companies.
SMARTER TROUBLESHOOTING
AAR VP strategy, planning & innovation Ryan Campbell gives a straightforward ranking of the innovations he thinks will be most important to improving aircraft maintenance in the next three years. His top three changes involve basic AI, predictive maintenance and the new generative AI (Gen-AI).
Next, in Campbell’s view, will come smarter computer-assisted troubleshooting, drones for inspecting aircraft and robotics for doing repairs. Then come two techniques accelerated by pandemic lockdowns and travel restrictions: remote repair assistance via virtual and augmented reality, and remote inspections.
Campbell believes optimizing heavy maintenance workflows and diversification of maintenance providers, for example into asset management, will also be important, as will increased digitization of maintenance processes and records. Additive manufacturing finishes his short-term list of innovation priorities.
Longer term, perhaps over the next 10 years, Campbell believes blockchain will finally come into play, and mergers and acquisitions among MRO providers will help, as will autonomous vehicles, that is tugs, for moving aircraft.
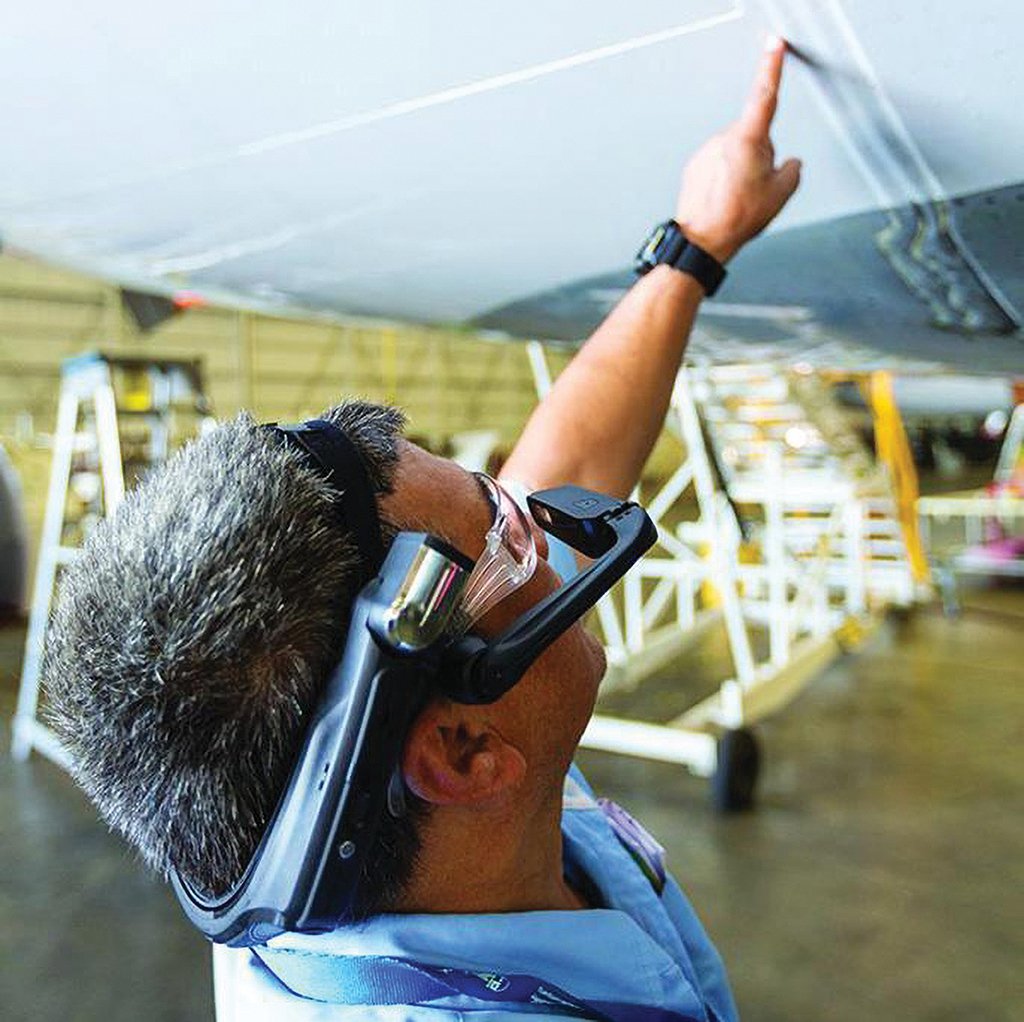
More generally, Campbell believes airline MRO is on the edge of a digital revolution.
“The growing need for digitization and innovation has led to the genesis of thousands of ideas coming from the most mature of companies to startups,” he said.
Digitization should therefore have a profound impact on an industry now dependent on archaic processes and technologies.
AI-driven predictive maintenance and advanced diagnostics will enable AAR to predict problems before they occur, Campbell believes. These proactive methods will minimize disruptions and improve safety. Other innovations will get aircraft back to airlines with faster turnaround times and fewer issues.
The US-based but now-global MRO provider is working on several innovative fronts. It is developing drones for inspections, deploying digitized workflow management to reduce paper-based task cards, and using virtual and augmented reality to guide training and inspections.
And AAR is upgrading its hangars with the IT infrastructure to handle more connected devices and investing in repair robotics. Finally, it is researching optimized workflow and inventory management, and exploiting Gen-AI.
ATS senior director-airframe bids Jon Morgan similarly checks off the innovations he views as most important.
“Predictive maintenance is already being used by most airlines, helping to better predict costs and lower turn times by pre-positioning parts and engineering,” Morgan said.
He called attention to optimizing heavy maintenance workflows, which saves cost and downtime, and increased digitization of maintenance processes and records. “Plus, the industry is going digital with paperwork signoffs,” he noted.
Morgan thinks diversification of maintenance providers, for example into asset management, will be important in supporting customers looking for one-stop shops. He says mergers and acquisitions will help provide simpler supply chains for airlines.
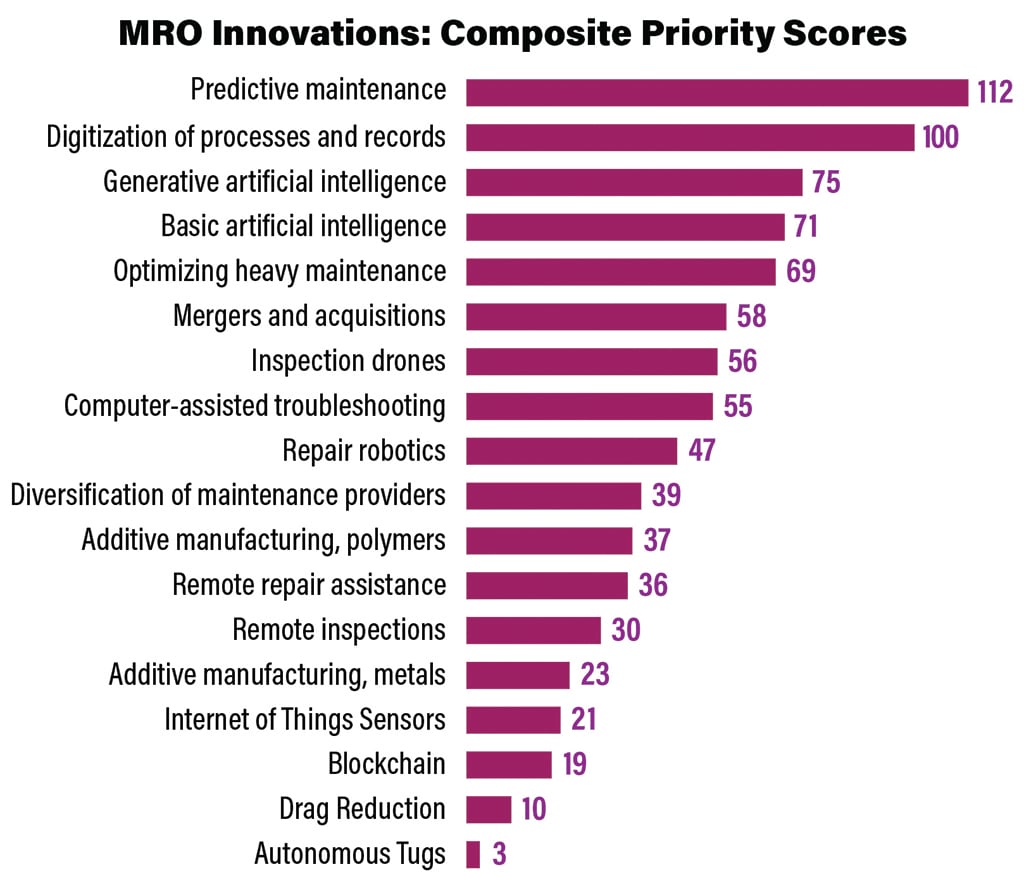
But Morgan selects optimizing maintenance workflows and increased digitization as the innovations most important to improving aircraft maintenance. He noted that ATS now manages 70% of its heavy maintenance and all of its component repairs with digital technology. The MRO provider has also identified strong processes for optimizing maintenance workflows.
ST Engineering SVP innovation Lee Hui Fung sees digitization, optimization of heavy maintenance, AI and Gen-AI as the most promising advances. Drones, robots, additive manufacturing, predictive maintenance and blockchain come next, in Lee’s view.
“Preset tolerance limits, when added to digital task cards, can prevent mechanics from inputting erroneous measurements,” Lee argues. Digitizing data also enhances analytics, boosting process optimization. And without good digital data, neither AI nor Gen-AI can work.
Since late 2017, ST Engineering has focused on digitization, data analytics, automation and additive manufacturing.
ST Engineering is digitizing across all functions—airframes, components and engines—and across locations. And it is exploring use cases for Gen-AI. Analytics is improving forecasting and planning and optimizing inventories. Data analytics can also aid predictive maintenance for engines and components. But Lee cautioned that unless all parties pool relevant data, “predictive maintenance will not lead to meaningful outcomes in the short term.”
ST Engineering has used additive manufacturing to meet part demand even during shortages and is expanding its catalog of additive cabin parts. Robotic drilling on floor grids for freighter conversions has reduced labor and improved productivity. Lee says automated drilling of fuselages is possible.
INSPECTION DRONES
AFI-KLM E&M director-innovations Ahmoss Messayeh says his primary short-term innovations will be predictive maintenance, including AFI’s Prognos suite; AI, which can extract insights from reports and flight logs quickly; and computer-assisted troubleshooting, which will use AI to guide technicians through diagnosis and repairs.
Inspection drones will also be important. “Collaborative robots, or cobots, are transforming inspections … performing visual inspections of aircraft surfaces,” Messayeh said. Digitization boosts efficiency and helps AI to further improve operations.
Longer-term, Gen-AI will use historical failures to predict when maintenance is required, train employees to give smart answers to questions quickly and optimize supply chains. Autonomous or remotely operated robots could conduct maintenance tasks in challenging environments.
Messayeh predicts remote assistance will lead to better complex repairs in far-flung regions, and better planning tools will further optimize heavy maintenance, cutting aircraft downtime. He believes blockchain will grow in importance in recording transactions and tracking assets. AFI-KLM E&M has therefore partnered with a blockchain provider.
Lufthansa Technik (LHT) says its top short-term priorities are predictive maintenance and digitization. Next come Gen-AI, remote inspections, additive manufacturing of polymers, diversification and mergers.
Over the longer term, LHT still sees predictive maintenance and digitization mattering most, followed by Gen-AI, remote inspections and additive manufacturing of metals. The MRO provider’s AVIATAR platform already offers a significant number of maintenance predictors for various aircraft and components. To broaden prediction capabilities, LHT is cooperating with airlines and part OEM providers such as Honeywell.
LHT has more than 100 digitization projects underway and is seeking a digital technical operations ecosystem by integrating AVIATAR with Swiss Aviation Software’s MRO application and flydocs’ digital records.
In the short term, Gen-AI could assist LHT mechanics by voice-recording findings into an AI device that understands the technical background and automatically generates new work scopes and instructions, plus connecting to tooling and part provision, reaping enormous time and cost savings. Longer term, Gen-AI will conserve expertise as, unlike LHT mechanics, this software does not retire.
LHT managers see drones achieving real gains only when their flight paths and defect detection are completely automated.
Remote inspections will become increasingly important in reducing travel as 5G data links become robust enough to provide highly detailed images. LHT’s Virtual Table has already begun this practice.
Chiefly a line maintenance provider at more than 50 stations across Europe, Nayak Aircraft Services must take a very practical view of innovation potential. CEO Marco Smit puts predictive maintenance at the top of his list of short-term improvements and says Nayak is seeing more and more predictive recommendations.
“This helps us to schedule maintenance instead of working unscheduled,” he said.
Next in Smit’s view is smarter computer-assisted troubleshooting. “With increased frequency, aircraft are giving us digital information from the system to perform maintenance instead of analyzing and inspecting ourselves,” he said.
Nayak has a base maintenance hangar in Dusseldorf, and Smit sees potential in optimizing heavy maintenance.
“Workflows in a maintenance environment can be optimized with enterprise resource planning software, plus knowledge, to be more efficient,” he said.
Other innovations will increase in importance over the longer term, in Smit’s opinion. He puts basic AI in this category, with AI helping with troubleshooting. But Smit thinks it may take years for this aid to be trustworthy enough for aviation. He judges Gen-AI as equally promising but needing to prove its reliability.
Smit has hopes for drone inspections enabling better and faster visibility of difficult areas of aircraft but stresses drones are still difficult to use at airports.
Both remote repair assistance and remote inspections also have long-term potential for assisting mechanics on the ramp, in Smit’s view.
Engine MRO has been preoccupied recently with problems affecting the Pratt & Whitney GTF. But engine shops are also looking to the future for innovations that will help them do the routine work of overhauls better and more economically.
StandardAero SVP-information technology Alejandro Mayoral said his short-term focus is on digitizing maintenance records and processes.
“The technologies needed already exist and can be incorporated relatively quickly.” he said. Mayoral thinks mergers or acquisitions by MRO providers will allow smaller companies to get capital and digital solutions from larger companies and thus accelerate digitization.
PREDICTIVE MAINTENANCE
Mayoral is a big fan of predictive maintenance, which started with engines. He believes predictions will continue to improve as performance data increases and AI models advance.
He also sees the new Gen-AI tools providing immediate value across several business functions, such as legal, human resources, finance, procurement, marketing and sales. Longer term, Mayoral expects Gen-AI to automate supply chains intelligently, find patterns that disrupt efficient work, address maintenance problems early on and generally increase productivity.
StandardAero director of sales & marketing business intelligence for airlines and fleets Alex Youngs supports Mayoral’s views. Youngs puts predictive maintenance at the top of his innovation list, noting his company has been using predictive tools to support engines for over 15 years.
“The application of AI to predictive maintenance should extend benefits further, ultimately enabling airlines to reset their assumptions relating to part inventories, tooling requirements and shop visits,” he said.
Next is digitization of maintenance processes and records. Digitization is not as exciting as other technologies, but benefits are significant, Youngs said.
“The ability of tablet-equipped technicians to access all processes and historical records on a specific engine serial number is extremely helpful, in terms of both operational safety and time savings, especially for field service reps,” he said.